Fitting Micarta Knife Scales – How To Do It Yourself
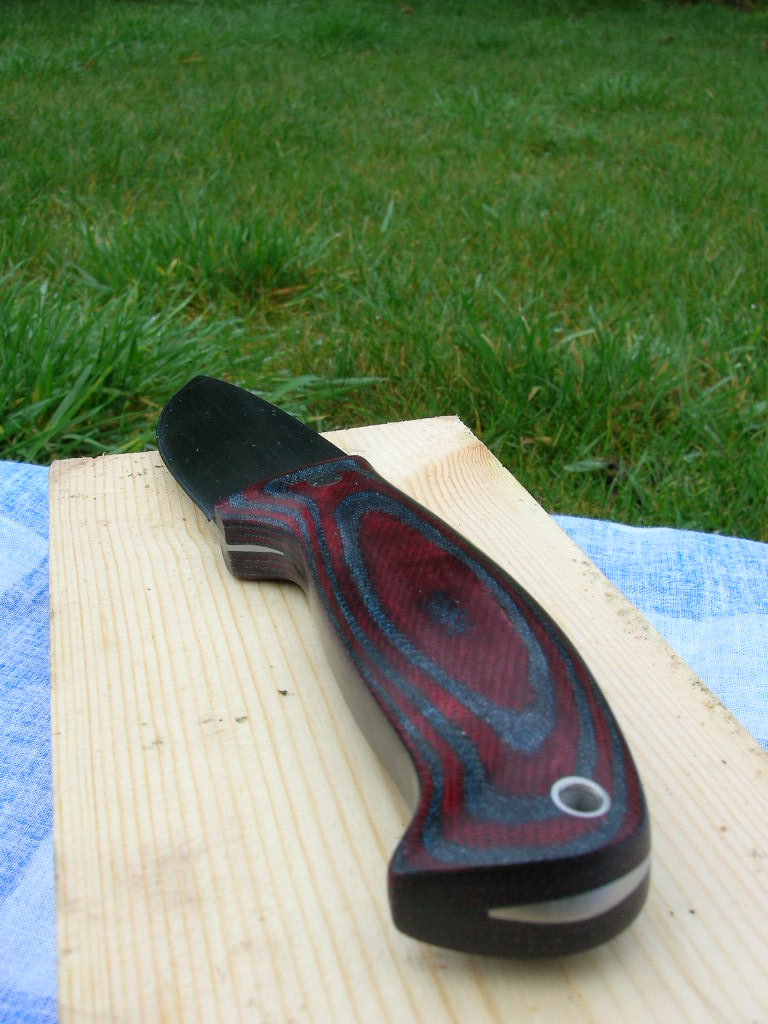
Over the last few years I have made a number of fixed blade knives by molding home made micarta directly to the tang of the knife. I have made full tang knives bolstered knives and stick tangs, mostly successful if not perfect.
Micarta is a brand name for composites of linen, canvas, paper, fiberglass, carbon fiber or other fabric in a thermosetting plastic. It was originally used in electrical and decorative applications.
Micarta was developed by George Westinghouse at least as early as 1910 using phenolic resins invented by Leo Baekeland. These resins were used to impregnate paper and cotton fabric which were cured under pressure and high temperature to produce laminates.
In later years this manufacturing method included the use of fiberglass fabric and other resin types were also used. Today Micarta high-pressure industrial laminates are produced with a wide variety of resins and fibers.
The term has been used generically for most resin impregnated fiber compounds. Common uses of modern high-pressure laminates are as electrical insulators, printed circuit board substrates, and knife handles.
The simplest handle to make is on a full tang blade. Putting a handle on a stick tang is very similar, so I will cover both these methods in this tutorial. Bolstered full tang knives I will cover later if people are interested. Bolstered stick tangs I haven’t managed to make reliably yet!
I am nowhere near to perfecting the technique but how I do it is simple and reliable. I hope others will give it a go and try out some new ideas too.
Here are some of the knives I have made using this technique and while preparing this Tutorial
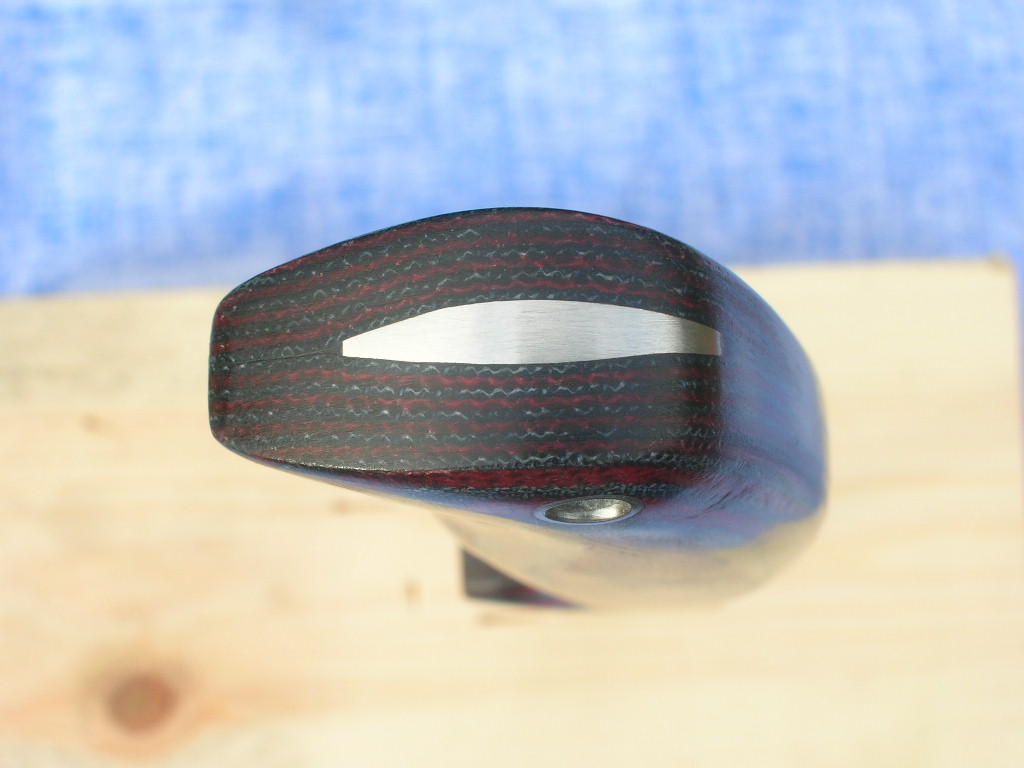
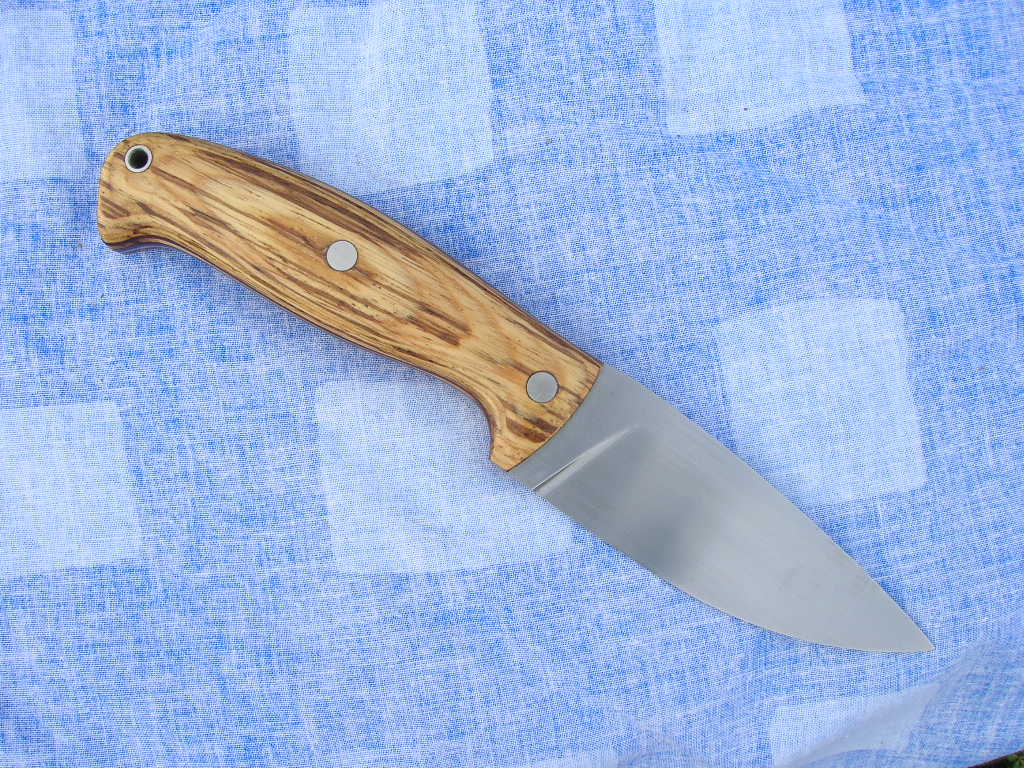

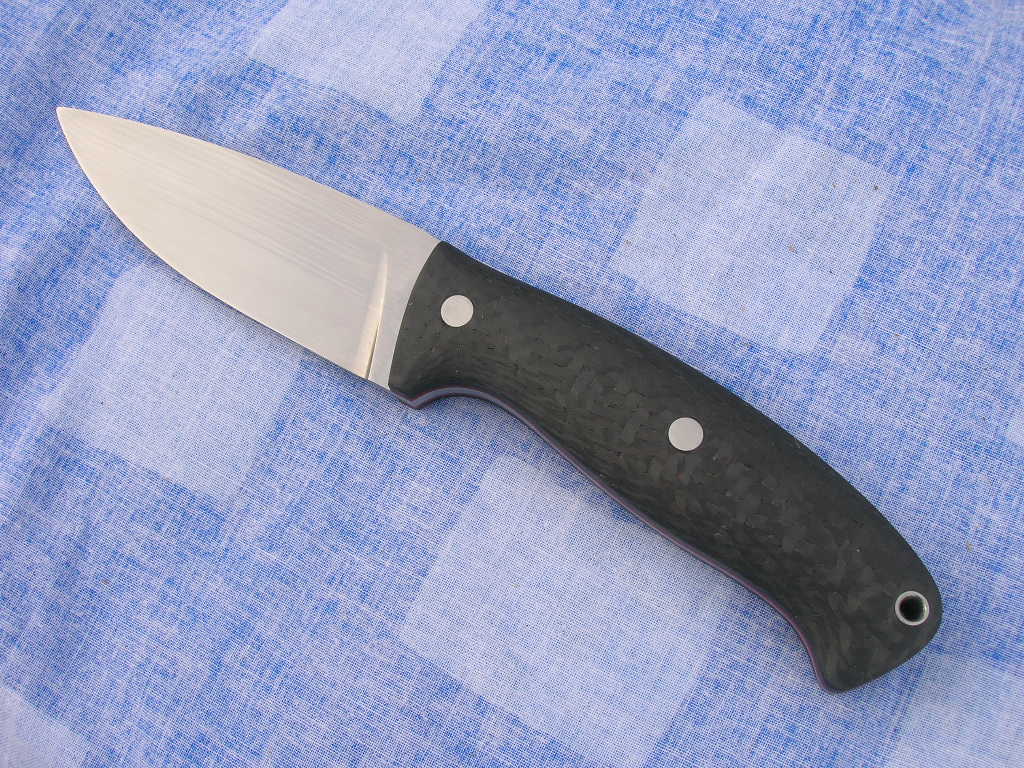
I will start with the actual molding process. I will add the boring but useful details later; please read them if you are going to have a go!
You will need the following – get it all ready to avoid running around the house with sticky fingers.
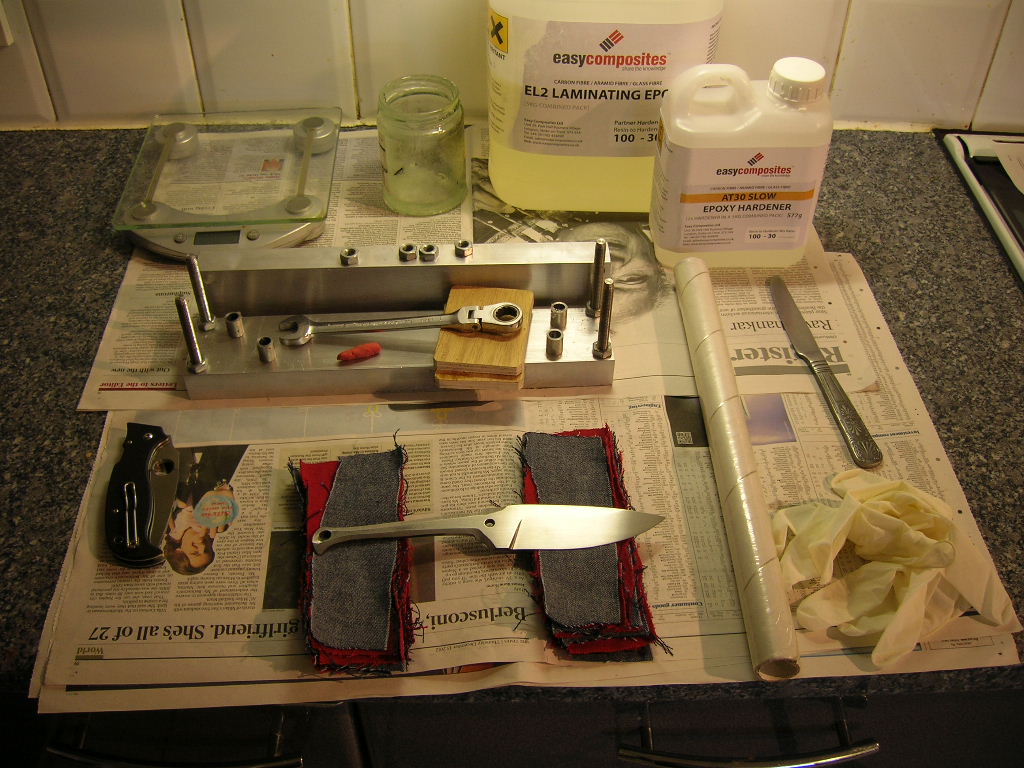
Resin + hardener
Scales or graduated container for measuring out resin
Jam jar or something similar for mixing resin
Stirrer/spreader – I use an old knife
Cling film + sharp knife to cut it
Micarta Press and spanner if required
Spacers
Cloth pieces.
Plasticine/Modeling clay – you don’t need much
Latex or Nitrile gloves
Knife blank fully finished and heat treated
1 Before you mix up any resin cover the top and bottom plates of your press with a layer of cling film. Make sure there is enough to accommodate excess resin. You don’t want resin stuck all over your press.
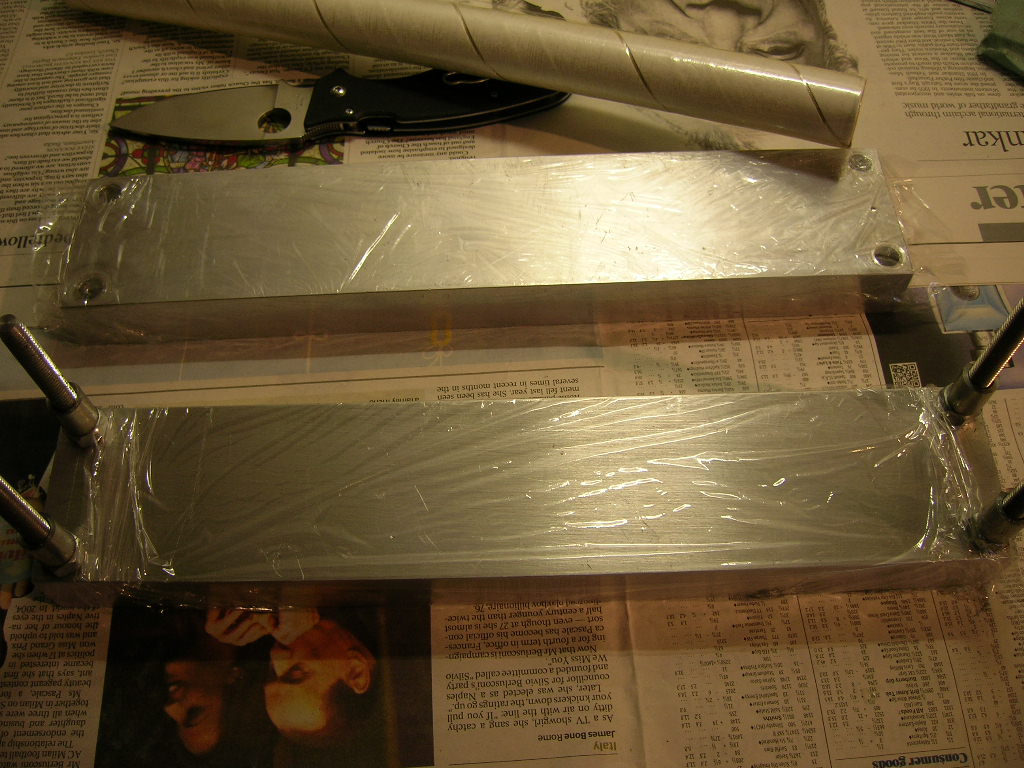
2 Put a small piece of plasticine in each hole in the tang of your knife. This is to stop the laminate molding too far into the hole and splitting the cling film. Don’t completely fill the holes as you want some interlocking to occur.
3 Mix about 150 grams of resin. This will be more than enough for an average sized handle. You could get away with less but to start with don’t scrimp.
4 Take half of your cloth pieces and one at a time, place them onto the lower part of the press in a stack.
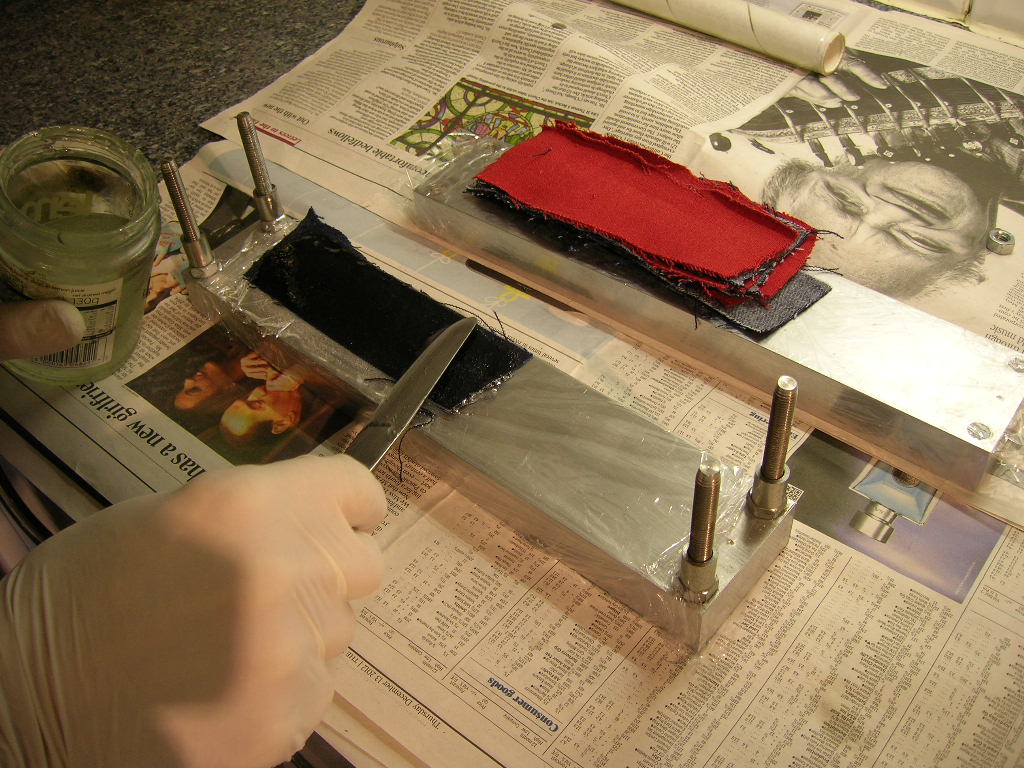
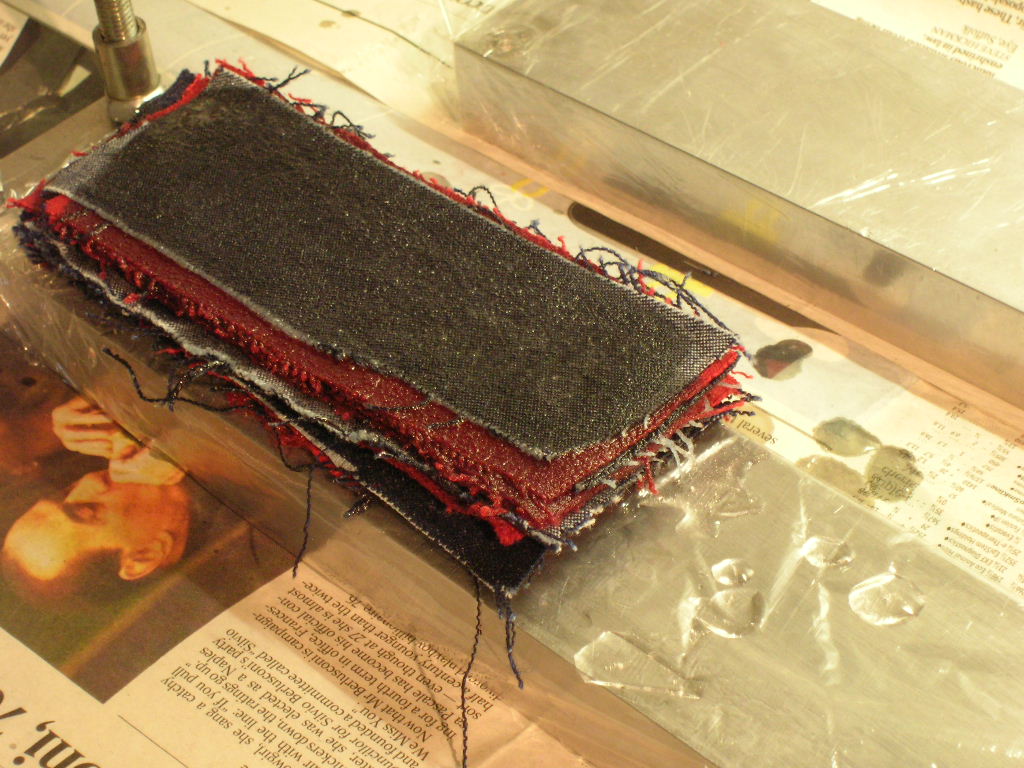
Wet each layer with resin as you go. Align the front edge and the top edge of each piece so when you have finished you have two neat datum edges.
5 Place a layer of cling film over the stack of fabric pieces.
6 Place your blade blank on top of the clingfilm on top of the stack. Align the top and front edges of the handle 5mm or so from the two neat edges of your stack. Assuming you cut all your cloth pieces big enough this will ensure you get complete scales with no gaps. With a stick tang it is worth using a template of the finished handle shape to check you have not placed the tang too near the edge of the stack.
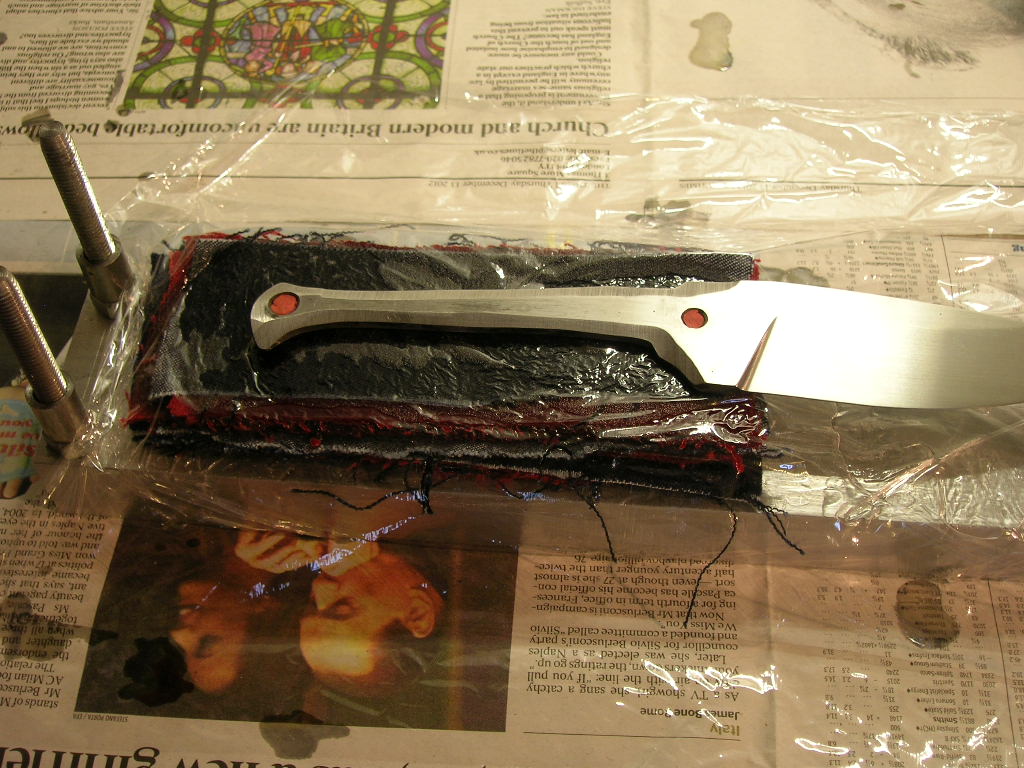
7 Place another layer of clingfilm over the blank.
8 Take the remaining cloth pieces and stack them (with resin as before) on top of the blade blank ensuring the two neat edges are aligned with the first stack.
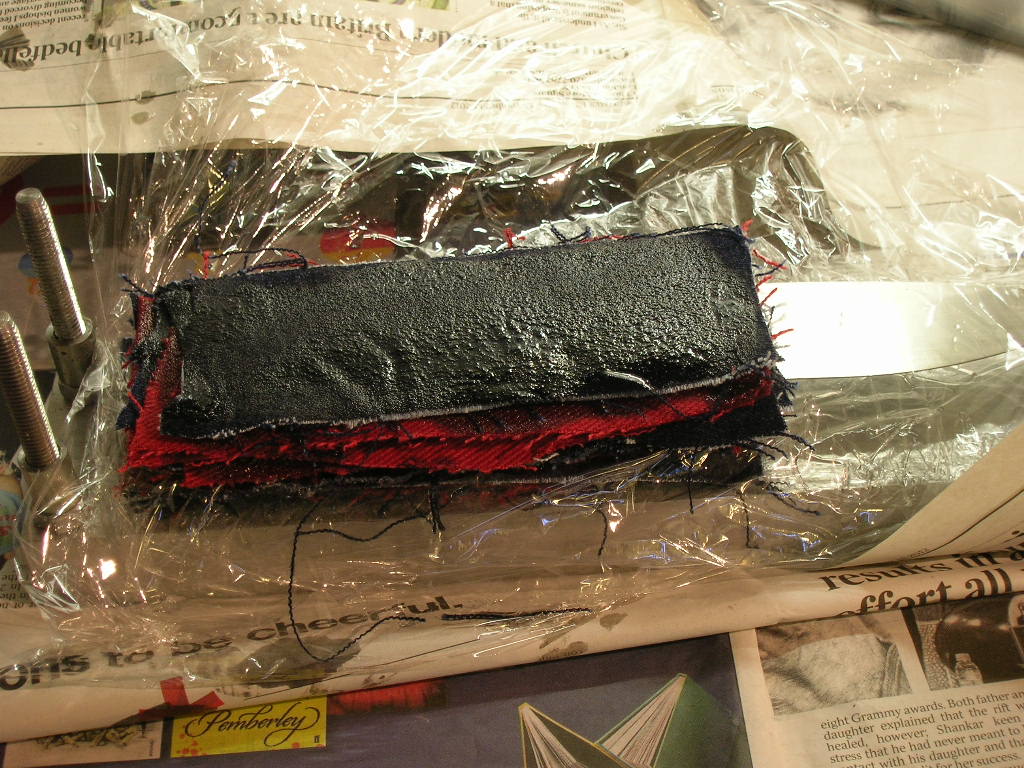
9 Take the top half of your press and tighten it down evenly, ensuring nothing slips. Tighten it evenly until you reach the correct thickness. If you have spacers, use them to keep everything parallel and the correct thickness.
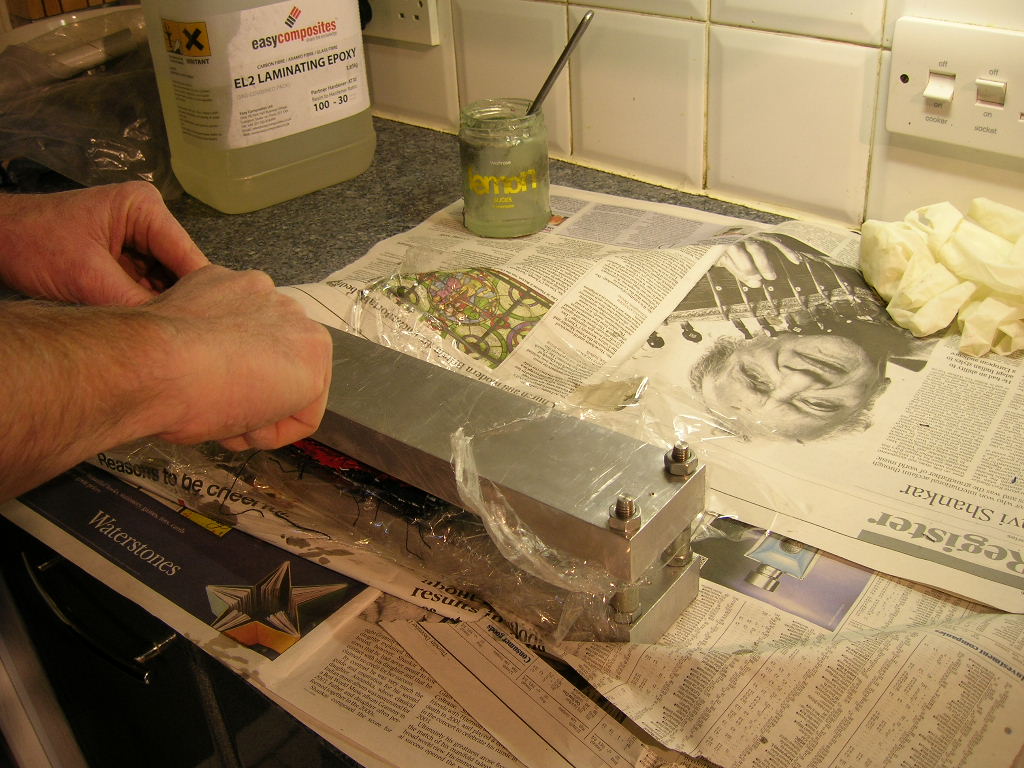
10 Give it plenty of time to cure; excess resin will dribble out at first so be careful. Make sure it is fully cured before opening the press. If it is not fully cured the scales could warp and loose the close fit, also it will be difficult removing all the clingfilm.
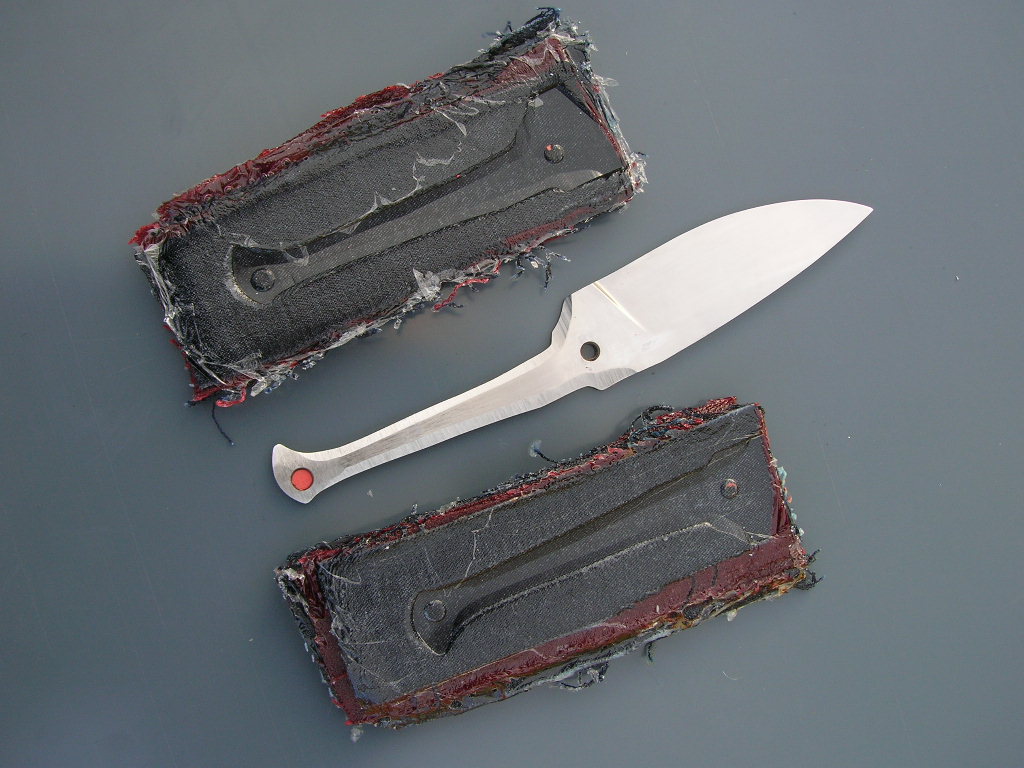
11 When the resin is rock hard, open the press and remove the knife. Prise the two scales off the blade and peel off all the cling film.
12 Trim the scales close to the finished shape. I do this one scale at a time with the tang located in its impression to show where to cut.
13 Finish up the front edges of the scales, make sure all traces of cling film are removed, key the surfaces and pin and glue on the scales. When cured shape and finish as you would any knife handle.
Knife Design – Full Tang Knife
The blade blank need be nothing more complicated than for any other construction method. It doesn’t need to be perfectly flat as the handle will mold into any imperfections, in fact, any shaping of the tang should make the scales a more secure fit as they wrap around and interlock the tang.
If you have drilled the tang, the micarta will ‘dimple’ into the holes making for a secure fit. If you want to taper the tang you can do and it doesn’t matter where you start the taper.
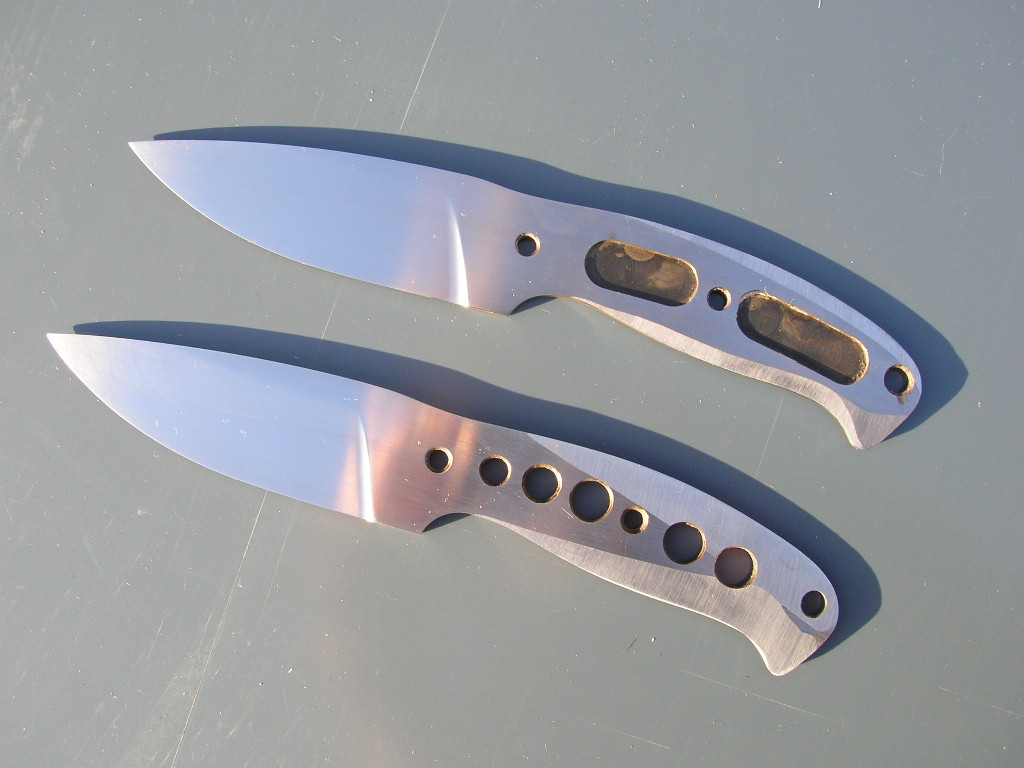
Here are a couple of example blade blanks that are ready for scales. The first one has been drilled and beveled to give a tapered look to the tang; the second one has been milled and beveled. The milled slots ensure very secure fitting scales.
You will notice the bevels are much wider on one blank than the other, this is up to you, a shallower angle removes more metal making your knife lighter and moving the balance point forward.
Knife Design – Stick Tang Knife
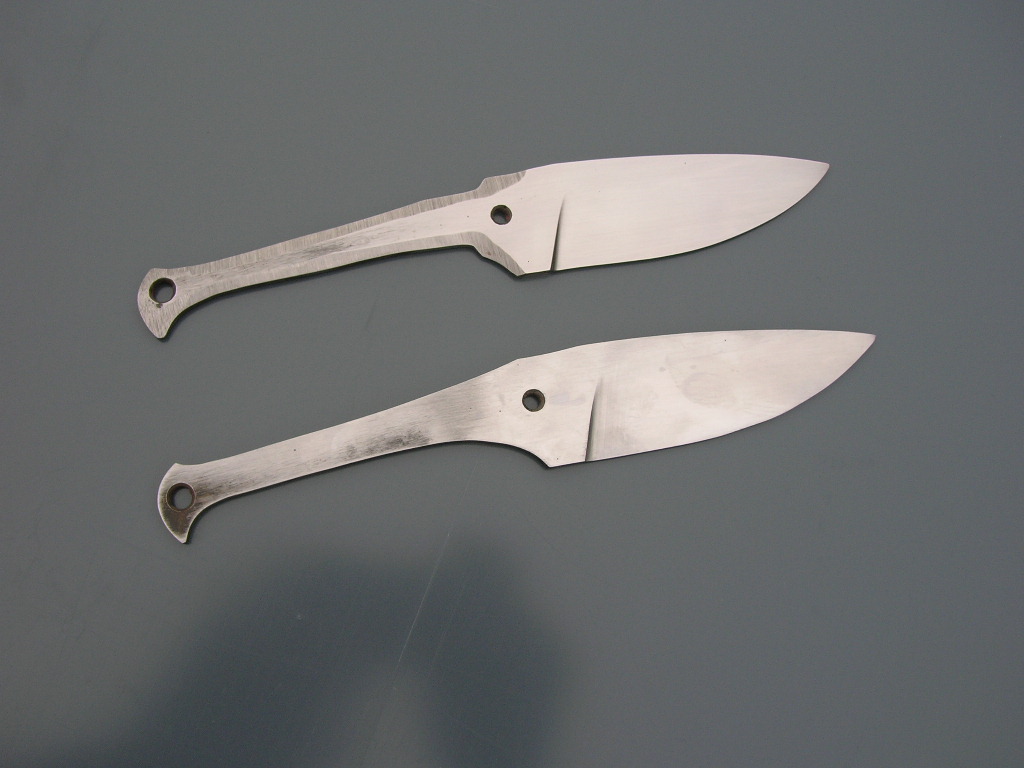
This is a little more complicated as at some point the tang must disappear into the micarta and we must avoid thin sections of micarta that will be vulnerable to knocks.
There is a limit to how much micarta will mold around corners and over steps so edges should be beveled and where the tang disappears it should be tapered, so the micarta halves flow together smoothly.
I find steps up to 2mm don’t cause a problem, any small voids where the micarta didn’t reach will be filled with epoxy and disappear when the scales are bonded together.
This picture shows two blanks; the upper one has been beveled to allow the micarta to flow around the tang. This shows up better on a finished knife.
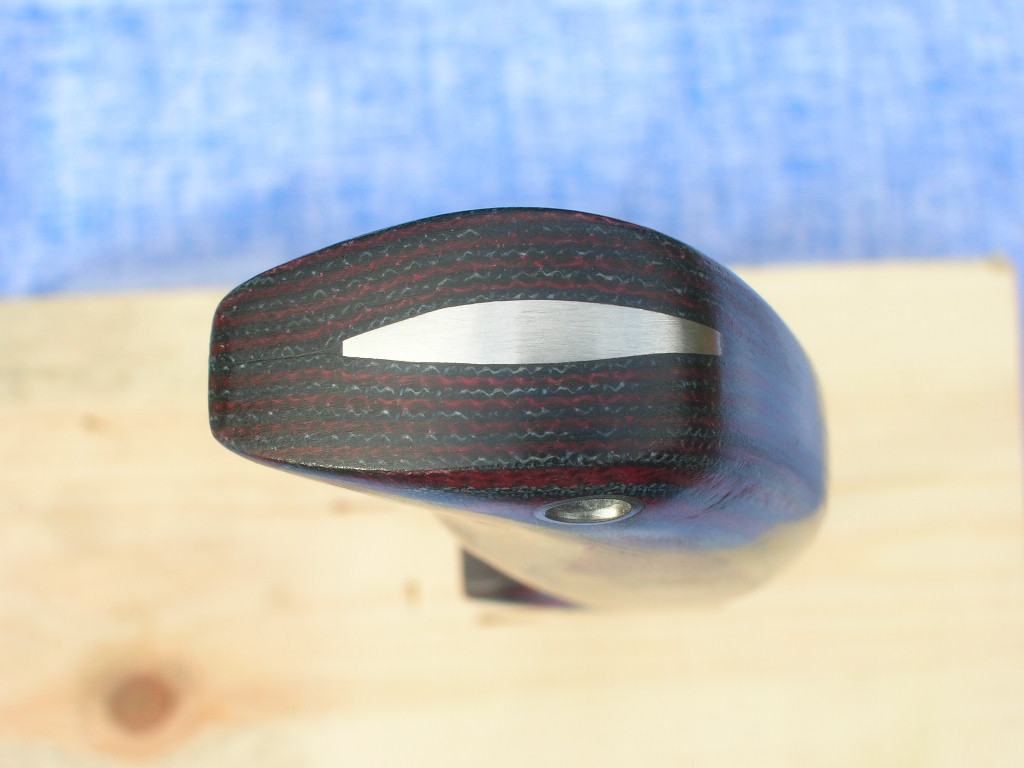

The end of the tang does not have to be flared like the examples and could be stopped short so it cannot be seen. Alternatively, it could protrude from the handle if you want to form a lanyard eye or a glass breaker.
Micarta Press
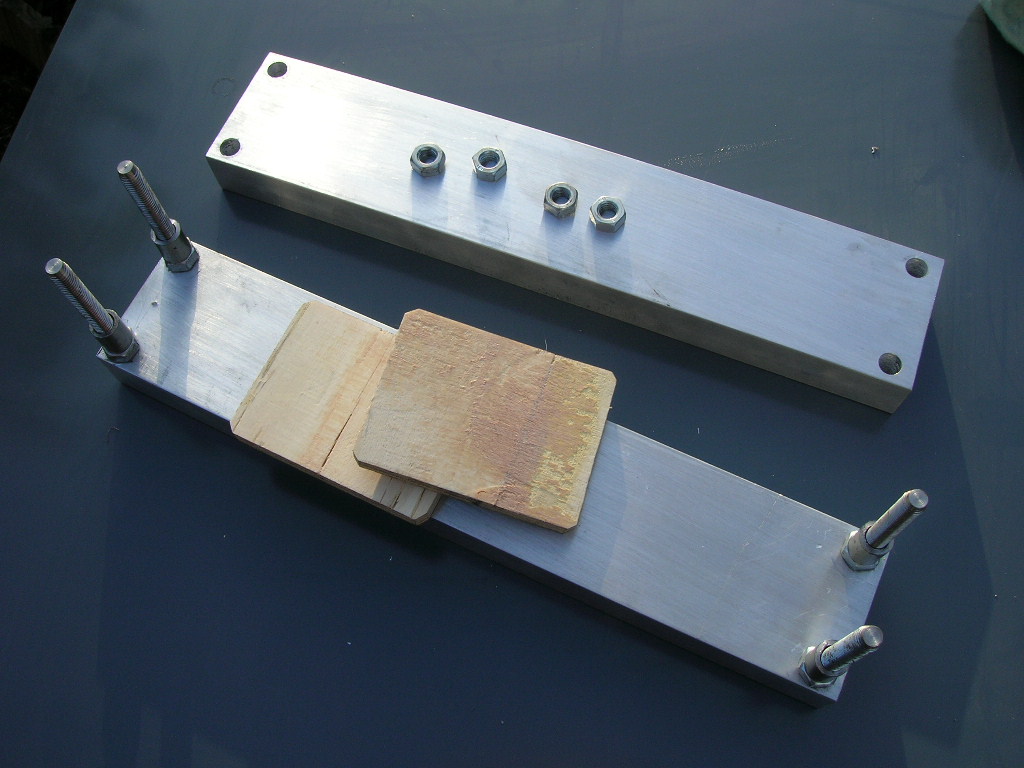
I have recently built this dedicated micarta press, but you can get by with the following:
1 Two flat, smooth and rigid surfaces a bit larger than your handle (50 to 75mm longer and 25mm wider should be big enough)
2 Some method of clamping these together. This could be G cramps or 2 to 4 pieces of studding through holes in your two plates. If you use the studding make your plates a bit bigger, so you have space to drill the holes.
3 Spacers to control the finished width of the laminate. These could be wooden blocks or if using 4 lengths of studding, lengths of tube to fit over the studding. The spacers should be a bit wider than the desired width of your finished handle (scales plus tang).
4 Spacers to center the blade. These are optional, but I would recommend using them to eliminate a possible source of error. In my experience, when molding scales the tang stays central giving even parallel scales on both sides.
If you put a spacer block either side of the blade it will be centralized when you tighten down the press. These spacers need to be something that will not mark your blade, and they need to be the same width as the desired width of the finished scales.
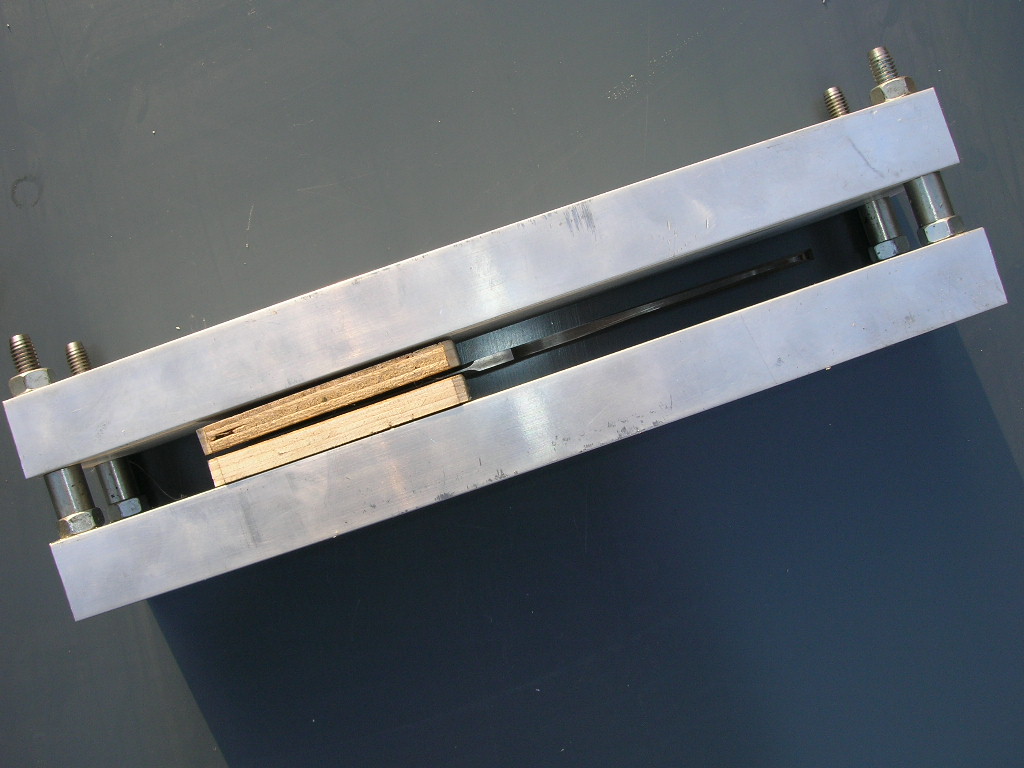
Micarta
To make micarta we need resin and cloth. There are all sorts of combinations of these and I have tried only a few. This is what I have learned.
Resin I have only used Epoxy laminating resin and have not had a single problem with it. Polyester is much cheaper and more readily available (Halfords) but it does stink so you can’t use it indoors unless you are single – or want to be. In the winter it is a big advantage working indoors as the temperature is much more consistent, and you will get consistent and reliable cure times. I have used the West System Epoxy and Epoxy from easycomposites.co.uk which is just as good and a bit cheaper.
Epoxy might seem expensive but when you workout the cost per knife it is not a lot! Use the slow hardener, so you have plenty of time to work.
Cloth
The only cloth I have tried and wouldn’t recommend is felt, it looked awful and did swell a bit after a month in the dishwasher.
Cotton, denim and linens are a good place to start and finish easily. Linens give a rougher grippier finish.
Carbon doesn’t flow around corners very well so I wouldn’t use it on stick tangs. Also, the cloth is very fragile, particularly when cut small, so there is a lot of wastage. Carbon eats coping saw blades and I haven’t yet managed to use it without getting small voids in the laminate. Also, it made me itch and gave me tonsillitis so make sure you use a mask. It does look good, but I wouldn’t recommend you start with this material!! You have been warned.
I have tried various other unidentified materials and they all worked fine, some looked better than others and they usually come out darker than the original material.
Patterned materials can look good (woven not printed) When selecting a material try and envisage how the different colored threads will look from the side top and end (like the grain of wood), you can alter or alternate the orientation and angle of the material to change the finished appearance of the micarta. You can combine all sorts of different materials; I have tried wood veneers and I have even seen people using stainless steel mesh!
You can’t beat denim for your first go.
When you have chosen your cloth you need to cut it to size. Cut pieces about 10mm wider all round than your desired handle size. How many pieces you need will depend on the thickness of the material and your scales. I cut enough so that when squeezed in a micrometer it reads the desired scale thickness. Have a few extra ready just in case and divide them into two piles so you get the same number each side.
Pigment
You can add pigment to your resin to alter how the finished micarta looks. I have only done this once, adding red pigment to a blue denim laminate. It came out a striking Lilac color. See this thread if you are interested
Thanks to pieinthesky and ©BritishBlades for allowing us to use this article
If you have any comments then please drop us a message on our Outdoor Revival facebook page
We love this sort of thing on Outdoor Revival and we’ll be bringing you a lot more of it over the coming months, if you enjoy making or designing kit let us know about it on our FB page, we’re also happy for article or review submissions, we’d love to hear from you.